Industrial Handrails for Highly Corrosive Environments – Galvanised Steel, Stainless Steel, Aluminium
For industrial projects in corrosive environments such as the water, mining and resources sector, Moddex is the only practical solution. Its Tuffrail® range is not only ideally suited to meet the most challenging and dangerous of conditions, it is the only range that has the option of three materials. This gives specifiers the best handrails for the corrosive environments of the site. Those materials are hot dip galvanised steel, marine grade aluminium and 316 grade stainless steel.
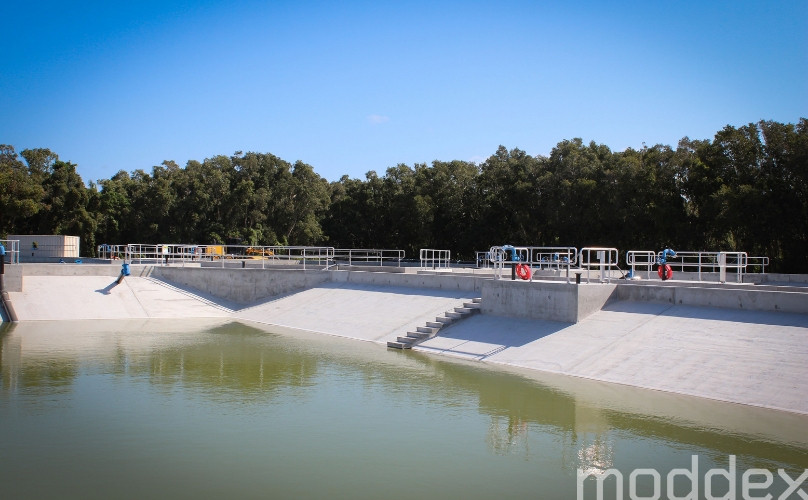
It is this last material, 316 grade stainless steel, that gives Moddex the edge. Moddex is the only modular stainless steel handrail for industrial applications available anywhere in the world. Modular galvanised steel handrails have existed for many years and more recently, some aluminium systems, but modular AND 316 stainless steel? Only available in Australia and New Zealand through Moddex.
Where Best to Use Tuffrail®?
Thanks to their ability to handle corrosive environments, marine grade aluminium and 316 grade stainless steel are commonly used in water and wastewater plants such as the Bondi Wastewater Treatment Plant. Located approximately 40 metres underground, its massive raw sewage pits are arguably one of the worst places in Sydney! Moddex’s 316 stainless steel Tuffrail® is the only handrail that can cope with such demanding, corrosive conditions.
The fact that Moddex handrails and balustrades are modular meant that components could be delivered and assembled on-site. This means avoiding dealing with the challenges of getting bulky pre-fabricated assemblies down the shafts of the wastewater treatment plant.
Oil rigs are another extremely difficult environment where Tuffrail® excels – for three reasons:
- Stainless steel handrails can withstand being doused with sea spray every day.
- Fabricated handrails that need to be welded can be tricky and expensive to air-lift out to rigs because of their size. Pallets of modular components are much easier to transport.
- Welding in such a flammable environment is both dangerous and expensive. Expensive because of the need for a partial site shutdown for the duration of the welding. There are also a large number of procedures that need to be followed to ensure workers’ safety.
Tested for Endurance
In a 1000-hour salt/acid fog booth test, the Moddex 316 grade stainless steel outperformed three other materials, looking just as good at the end of the test as it did at the beginning – and just as sound.
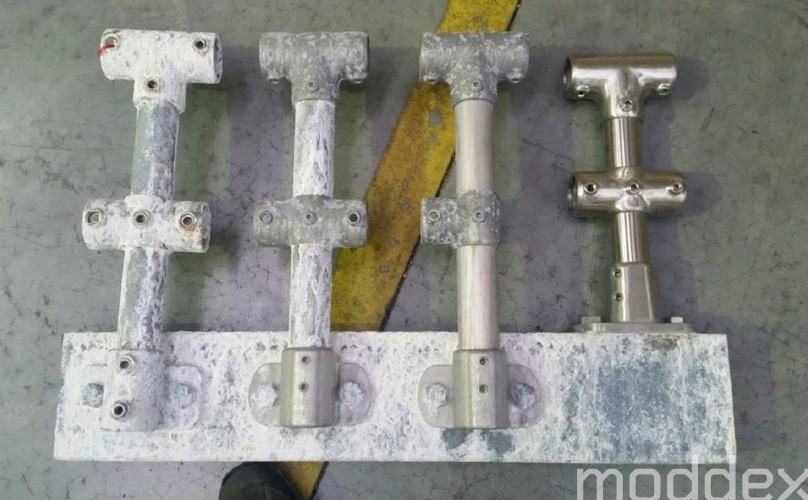
One other thing that’s important to know about Moddex Tuffrail® handrails – they are designed to last much longer than the planned lifetime of many infrastructure projects. Where, for example, a wastewater plant is built to survive 25 years, at the end of that time 316 stainless steel Moddex Tuffrails® will still be performing at optimum levels – and will go on doing so for another 75! Building such long-lasting products is one of the many ways Moddex stands out above its competitors.
For companies looking to extend the life of their structures, a Moddex Tuffrail® modular system is the answer.
Enquire now